Stainless steel has excellent characteristics such as unique strength, high wear resistance, excellent corrosion resistance and not easy to rust. Therefore, it is widely used in the chemical industry, food machinery, electromechanical industry, environmental protection industry, household appliances industry and home decoration, finishing industry, giving people a gorgeous and noble feeling. The application and development prospects of stainless steel will become wider and wider, but the application and development of stainless steel largely determines the degree of development of its surface treatment technology
The technology of stainless steel surface treatment includes surface whitening treatment, surface mirror bright treatment, surface coloring treatment, etc.:
- Chemical oxidation coloring method: It is the color of the film formed by chemical oxidation in a specific solution, including dichromate method, mixed sodium salt method, vulcanization method, acid oxidation method and alkaline oxidation method. Generally, "INCO" (INCO) is used more, but if you want to ensure the same color and luster of a batch of products, you must use a reference electrode to control.
- Electrochemical coloring method: It is the color of the film formed by electrochemical oxidation in a specific solution.
- Ion deposition oxide coloring method chemical method: that is, the stainless steel workpiece is placed in a vacuum coating machine for vacuum evaporation plating. For example: titanium-plated watch cases and watch straps are generally golden yellow. This method is suitable for high-volume product processing. Because of the large investment and high cost, small batch products are not cost-effective.
- High temperature oxidation coloring method: In a specific molten salt, the workpiece is immersed in a certain process parameter, so that the workpiece forms a certain thickness of oxide film, and presents various colors.
- Gas-phase cracking coloring method: It is more complicated and less used in industry.
Stainless steel surface treatment:
- Cleaning and grinding: If there is any damage, it should be polished, especially the scratches and splashes caused by contact with carbon steel parts, and the damage caused by cutting slag must be carefully and thoroughly cleaned and polished.
- Mechanical polishing: Use appropriate polishing tools for polishing, requiring uniform treatment and avoiding over-polishing and re-scratching.
- Oil removal and dust removal: Before pickling and passivation of stainless steel parts, oil, scale, dust and other sundries must be removed according to the process.
- Water blasting treatment: According to different treatment requirements, different micro glass beads and different process parameters should be selected, and overspray should be avoided.
- Pickling passivation: The pickling passivation of stainless steel parts must be passivated in strict accordance with the process requirements.
- Cleaning and drying: After pickling and passivation, neutralization, rinsing and drying should be carried out in strict accordance with the process to completely remove the residual acid solution.
- Protection: After the surface treatment of stainless steel parts is completed, they should be well protected to avoid secondary pollution from personal touches and sundries such as oil and dust.
- Avoid reprocessing: After the surface treatment of stainless steel parts is completed, reprocessing of the parts or products should be avoided.
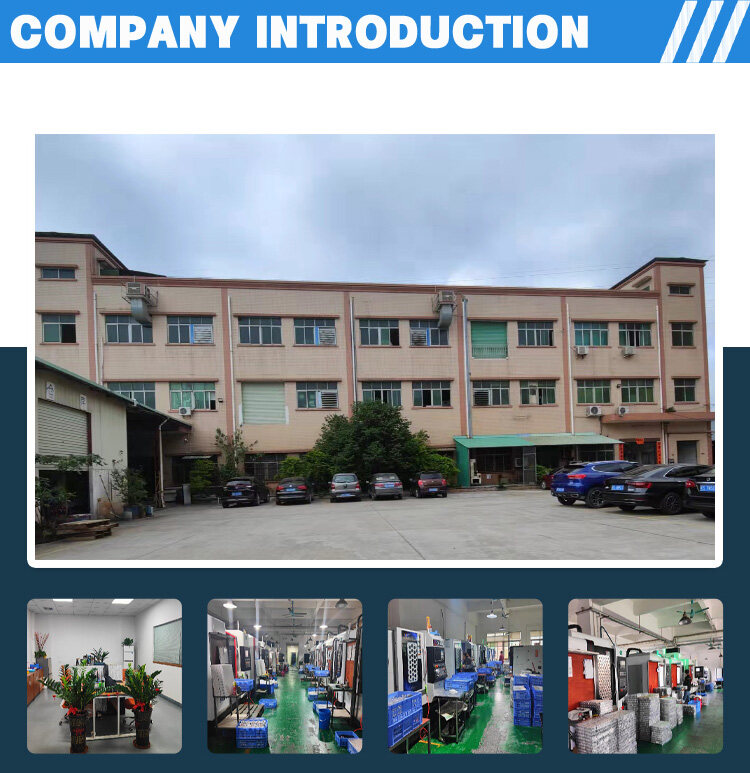
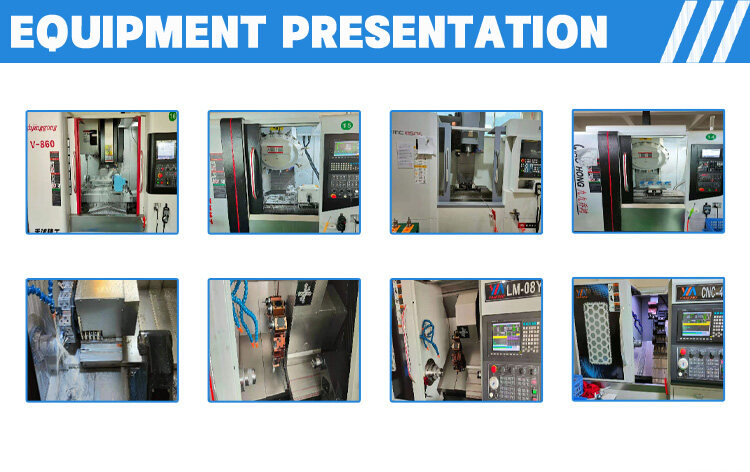
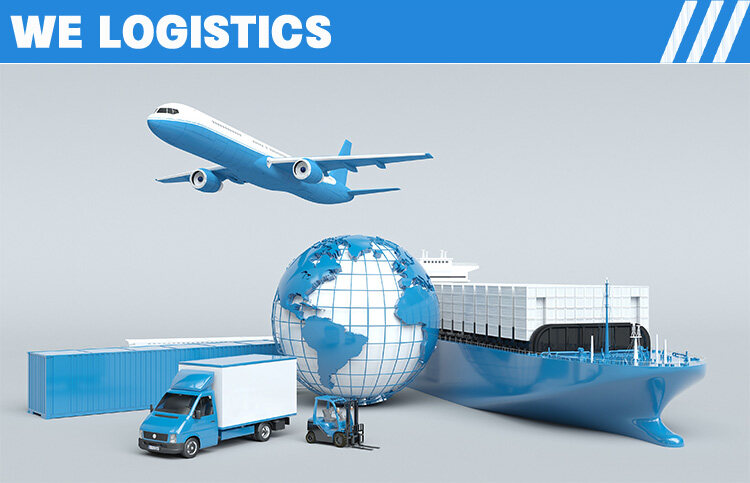